June 19, 2023
There is a Growing Trend among Major Chemical Companies to Make Plastic Raw Materials from Plant-derived Alcohol "Bioethanol"
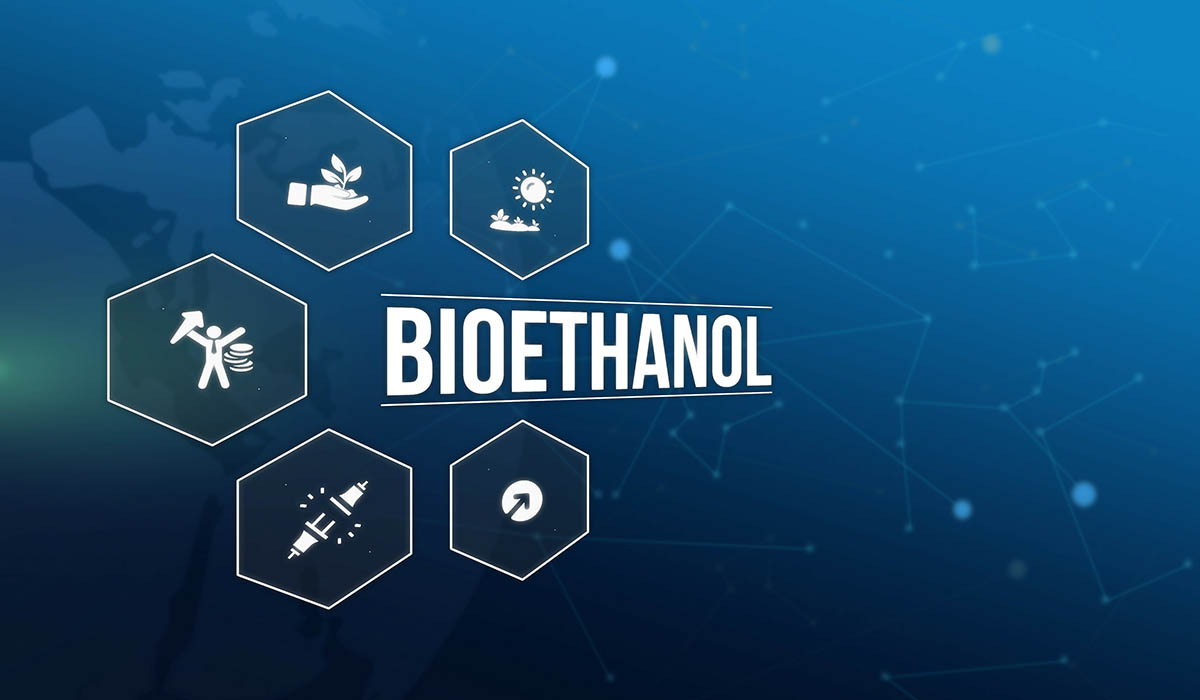
Asahi Kasei will begin domestic production in the 10,000-20,000 ton scale by about 2027. Sumitomo Chemical also plans to start mass production around 2025. Amid domestic and international demands to reduce carbon dioxide (CO2) emissions, it is hurrying to establish manufacturing technology for plant-derived plastics with a low environmental impact.
Asahi Kasei uses bioethanol, made by fermenting plant sugars, to make basic plastic raw materials. Ethanol can be reacted in a high-temperature environment with a catalyst that promotes chemical reactions to produce the basic raw materials ethylene, propylene, and toluene in a single process.
Plastic-related products that are difficult to recycle are most likely to be incinerated, and the entire biomass plastic process up to disposal can reduce CO2 emissions. Production costs will be verified.
Biomass plastics account for less than 1% of total plastic production, but global demand will multiply. According to the European Bioplastics Association, the production capacity in 2022 is 2.21 million tons, an increase of 24% from the previous year. It is expected to increase 2.8 times from 2022 to 6.29 million tons in 2027.
Depending on the resin type, biomass plastics are 1.5 to 5 times more expensive than those derived from petrochemicals. One opinion is "Price has been a barrier to widespread use. Policies to encourage use are needed". Efforts to expand applications in collaboration with home appliance and car manufacturers will be essential.